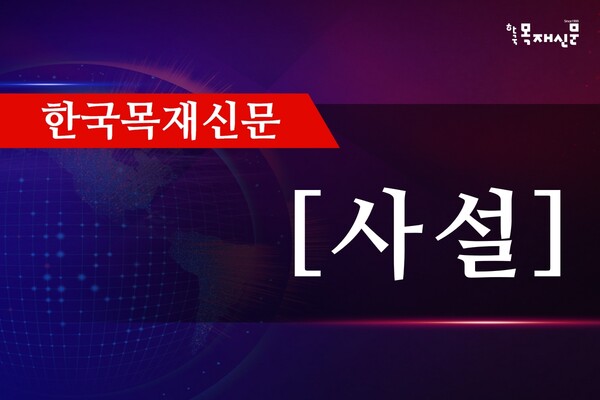
일본의 경우 합판생산을 위해 연간 약 550만㎥의 침엽수 원목을 투입하는데 대부분 평균 22cm의 삼나무나 편백을 이용한다. 이보다 직경이 더 큰 원목은 제재용으로 이용하고 직경이 작은 원목은 값싸게 사서 합판용으로 이용한다. 나머지는 바이오매스용이다. 제재와 합판용 원목은 81%에 이른다. 우리나라는 합판용은 0%, 제재용은 14% 밖에 안 된다. 이는 목재이용기술에 문제가 있음을 뜻한다.
일본의 합판회사는 33개나 되고 100% 가깝게 자국의 중·소경목을 이용해 합판제조 국산화에 성공했다. 일본은 끊임없이 합판기계를 개발하고 최적화해 가면서 국산합판시대를 열었다. 2001년 3%밖에 안 되는 합판제조 국산화율을 2020년에 91%로 높였다. 이렇게 되기까지 20년이 걸렸다. 일본은 지금 이 시간도 합판기계들은 지능화되고 안전성이 강화되고 피로감을 줄이는 진화를 하고 있다.
최근 닛신의 본사 신공장이 생산직 사원 70명이 소요되는 공장을 30명으로 줄였다는 뉴스가 일간목재신문에 보도돼 화제다. 10~15만㎥의 합판을 생산하는 공장에 70명이 근무하는 것도 대단한데 이를 절반 수준으로 줄이는 혁신은 하루아침의 결과일 수 없다. 우리나라의 합판회사는 90~100여명의 생산직 직원이 필요했다. 인건비만 해도 수십억 원의 차이가 발생하고 합판의 품질과 생산수율을 따지면 다시 수십억 원. 이 모두를 합하면 연간 100억 원 이상의 차이가 발생하게 된다. 국산원목을 투입해 생산수율이 10% 차이가 나면 10만㎥ 기준으로 1만㎥가 적게 생산되기 때문에 수율만으로도 50~60억 원의 매출 차이를 나게 한다. 합판의 설비는 그만큼 중요하다. 노후화된 합판의 설비투자를 포기한 순간부터 적자는 예견된 것이었고 새로운 설비를 도입하지 않는 한 그 한계를 넘는 건 어려운 일이다. 정부지원을 받거나 관세장벽을 높여도 이미 때는 지났다는 것이다.
합판뿐만 아니라 제재, 대패, 분쇄, 도장 등 대부분의 목재가공 설비는 수십 년 전의 것도 모자라 폐업한 회사의 것을 다시 사서 가동하는 것도 흔하게 볼 수 있다. 마루설비가 그 대표적인 예다. 시장 가격이 너무 좋지 못해 새로운 설비를 놓을 수가 없다는 말을 흔히 듣는다. 하지만 품질을 높여 소비자를 만족시키는 노력이 있어야 목재가공 설비도 발전할 수 있다. 설비투자가 멈춘 산업은 국가적으로 매우 심각한 신호다. 제조업이 회생 불가능한 수준으로 떨어지고 있음을 의미한다. 목재가공 후진국이라 하는 나라들도 매년 가공기계들이 발전한다. 하지만 우리는 목재제조업이 몰락하면서 목공기계산업도 동반 몰락했다. 기계를 고치는 사람도 부품을 생산하거나 가지고 있는 사람도 점점 찾기가 어렵다. 복잡하고, 손 많이 가 위험한 기계들을 작동할 사람마저도 모셔오기 어려운 상황이 됐다.
특히, 제조기반의 생산이 한계에 봉착한 점은 미래를 어둡게 하고 있다. 목재산업의 기업들은 늘 새로운 기계를 보아야 하고 필요하면 개발도 해야 하며 선진 목재가공기술을 파악하고 공유도 해야 한다. 심각한 건설경기침체에 따른 매출부진이 기업의 생존을 심각하게 위협하고 있지만 이보다 더 두려운 것은 산업자체의 혁신과 발전 가능성이 멈추는 것이다.
국산재의 이용은 과거의 방식보다 새로운 가공기술과 설비를 염두하고 발전해 가야한다. 과거의 제재방식, 과거의 섬유판 제조를 뛰어넘는 이용기술들을 습득하고, 필요하면 도입하거나 개발해서 우리 국산 원자재의 특성에 맞는 이용이 돼야 한다. 국산재 이용은 기후변화에 대응하는 탄소중립이용에 가장 현실적 대안이 되기 때문이다. 태우는 것은 적게 장수명 제품은 많게 국산목재자원을 최적화해 이용해야 한다.